In many industries, off-the-shelf equipment simply doesn’t cut it. Sometimes, you need something specifically tailored to your unique processes and requirements. That’s where custom fabricated equipment comes in. Designing this equipment can seem daunting, but by following a structured approach, you can create equipment that perfectly fits your needs and enhances your operations. This guide will walk you through the key steps involved in designing custom fabricated equipment.
Understanding Your Needs: Defining the Purpose
Before you start sketching or contacting fabricators, you must have a crystal-clear understanding of what your equipment needs to do. This stage is all about defining the purpose and functionality of your custom equipment.
Note: Custom fabricated equipment in the UAE provides tailored solutions for diverse industries, from manufacturing to construction, offering unique designs and precise functionality.
Identifying the Problem: What Needs Solving?
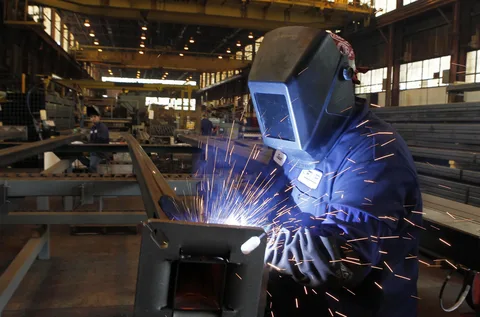
What specific problem are you trying to solve with this equipment? Is it to automate a process, improve efficiency, handle a unique material, or something else entirely? Clearly defining the problem is the foundation upon which your design will be built.
Defining the Functionality: What Should it Do?
Once you know the problem, outline all the functions the equipment needs to perform. Be specific. For example, if it’s a mixing machine, what materials will it mix? In what quantities? How quickly? What consistency is required? The more detail you provide, the better the design will meet your needs.
Operational Requirements: How Will it Be Used?
Consider how the equipment will be used in your workflow. Will it be a standalone unit or integrated into an existing system? Who will operate it? What are the safety requirements? Thinking about these operational aspects is crucial for a practical and user-friendly design.
Performance Goals: Setting Measurable Objectives
What are your performance goals for the equipment? Do you want to increase throughput, reduce waste, improve accuracy, or enhance safety? Setting measurable objectives will help you evaluate the success of your custom fabricated equipment.
Conceptualizing the Design: Bringing Ideas to Life
Now that you have a solid understanding of your needs, it’s time to start conceptualizing the design. This stage involves brainstorming, sketching, and exploring different design options.
Brainstorming and Sketching: Exploring Possibilities
Start by brainstorming different design concepts. Don’t be afraid to explore even seemingly outlandish ideas at this stage. Sketch your ideas on paper, even if they’re rough. Visualizing your concepts can help you refine them and identify potential issues.
Considering Materials: Choosing the Right Stuff
Think about the materials that would be best suited for your equipment. Consider factors like strength, durability, corrosion resistance, and cost. Different materials have different properties, so choose wisely based on the specific requirements of your application.
Developing a Basic Design: Putting it Together
Based on your brainstorming and material considerations, develop a basic design for your equipment. This could involve creating more detailed sketches or even using simple CAD software. The goal is to create a visual representation of your concept that you can share with others.
Refining the Design: Adding Detail and Precision
Once you have a basic design, it’s time to refine it. This stage involves adding details, making precise measurements, and ensuring that the design is practical and feasible.
Detailed Drawings and Specifications: Clarity is Key
Create detailed drawings and specifications for your equipment. Include precise measurements, material specifications, and any other relevant information. Clear and accurate drawings are essential for the fabrication shop to understand your design and build the equipment correctly.
Engineering Considerations: Ensuring Functionality and Safety
Consider any engineering factors that may affect the design, such as load capacity, stress distribution, and safety mechanisms. If necessary, consult with an engineer to ensure that your design is sound and safe.
Ergonomics: Designing for the User
Think about the ergonomics of the equipment. How will operators interact with it? Are the controls easy to reach and use? Is the equipment designed to minimize strain and fatigue? Designing for the user is crucial for safety and efficiency.
Choosing a Fabrication Shop: Finding the Right Partner
Once you have a finalized design, you need to find a fabrication shop that can bring your vision to life.
Researching and Evaluating Shops: Due Diligence
Research different fabrication shops in your area or beyond. Look at their portfolio, read reviews from previous clients, and check their certifications and accreditations.
Communicating Your Design: Clear and Concise
Clearly communicate your design to the fabrication shop. Provide them with detailed drawings, specifications, and any other relevant information. Be prepared to answer their questions and address any concerns they may have.
Getting Quotes and Comparing Prices: Value for Money
Get quotes from multiple fabrication shops and compare prices. However, don’t just focus on the lowest price. Consider the quality of their work, their experience, and their reputation.
Reviewing and Approving: Ensuring Accuracy
Before fabrication begins, review the final drawings and specifications with the fabrication shop. Make sure everything is correct and that you are satisfied with the design. This is your last chance to make any changes before the equipment is built.
Testing and Inspection: Quality Control
Once the equipment is fabricated, it’s important to test and inspect it thoroughly to ensure that it meets your specifications and functions as intended.
Functional Testing: Checking Performance
Test all the functions of the equipment to make sure they are working correctly. This may involve running simulations or testing the equipment in a real-world environment.
Visual Inspection: Checking for Flaws
Visually inspect the equipment for any flaws or defects. Check the welds, the finish, and all other details to ensure that the quality is up to your standards.
Documentation and Maintenance: Keeping Records
Keep detailed documentation of the design, fabrication process, and testing results. This documentation will be valuable for future maintenance and repairs.
Operating Manuals: User-Friendly Instructions
Create operating manuals for the equipment that are clear, concise, and easy to understand. This will help ensure that operators use the equipment correctly and safely.
Maintenance Schedules: Preventing Problems
Develop a maintenance schedule for the equipment to prevent problems and ensure its longevity. Regular maintenance is crucial for keeping your custom fabricated equipment in good working order.
Conclusion: A Collaborative Process
Designing custom fabricated equipment is a collaborative process that requires careful planning, clear communication, and attention to detail. By following the steps outlined in this guide, you can create equipment that perfectly fits your needs and enhances your operations. Remember that investing time and effort in the design process will pay off in the long run with equipment that is efficient, reliable, and tailored to your specific requirements.
For more insightful articles related to this topic, feel free to visit authenticdigital.in